QUALITY ASSURANCE
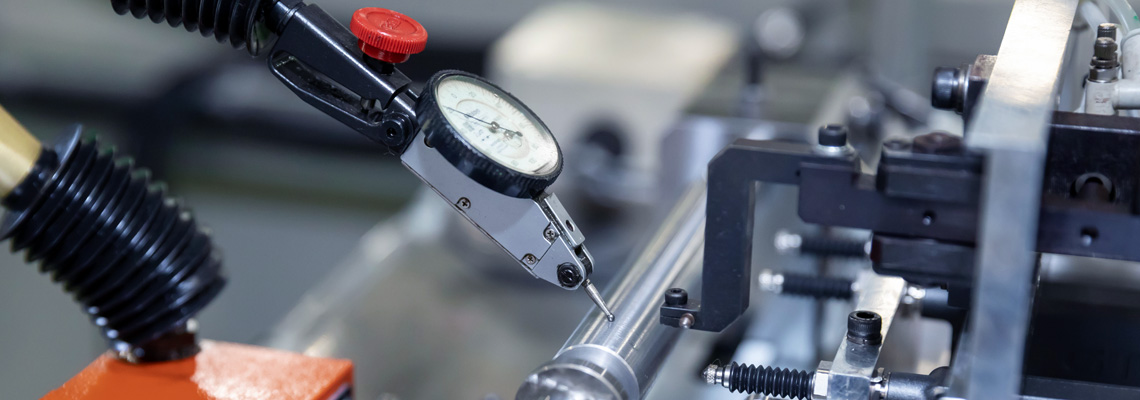
We aim to be the world’s top shaft manufacturer.
The shaft is an important functional component which has a complex shape, but is also required to be the highest quality in all aspects, including precision and durability. We must meet ever more difficult challenges in the face of rapidly advancing technological innovation. In response to these needs, our company aims to contribute to the future of Japan and the world as a specialized shaft manufacturer.
Shaping a factory floor that makes no waste. Quality is built into each and every process.
Kaneta Kogyo quality is built into each and every process in our factory. Workers and managers on the production line aim to keep any defects from being sent on to the next process, so they improve both their own work procedures as well as upstream processes in a system known as “upstream kaizen”. This keeps wasteful costs incurred from making defective products to a minimum.
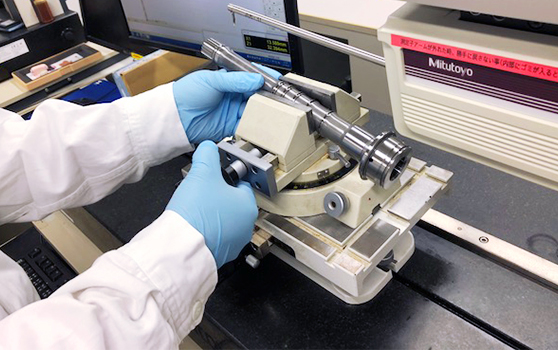
The highest quality, guaranteed by thorough quality management.
Shaft quality is an important element tied directly to the safety of an automobile.
For that reason, we conduct thorough quality management in order to always assure the highest quality. Our factory has a strict quality management system in place, using automatic detection equipment that check product dimensions at the micron level, such as laser measurement devices.
For that reason, we conduct thorough quality management in order to always assure the highest quality. Our factory has a strict quality management system in place, using automatic detection equipment that check product dimensions at the micron level, such as laser measurement devices.
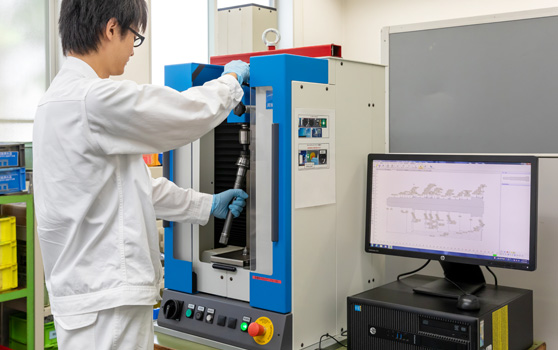
Quality assurance equipment optimized for the characteristics of each product is installed between each process.
Shaft products are often used as critical safety components and large load bearing components, so their most important points differ depending on their function or shape.
Kaneta Kogyo develops its own quality assurance equipment in-house, optimized for such specialized products, always aiming for higher quality with a unique approach.
Kaneta Kogyo develops its own quality assurance equipment in-house, optimized for such specialized products, always aiming for higher quality with a unique approach.
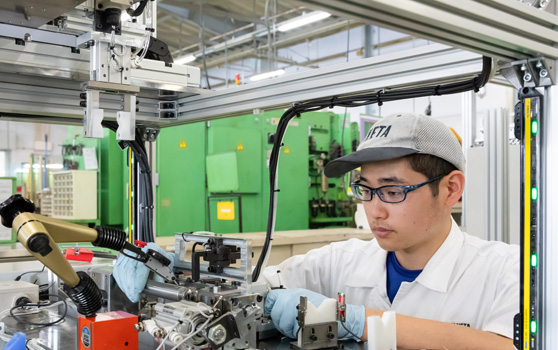
Bringing Japanese manufacturing technology to the world. We offer a global quality assurance system.
The head office of Kaneta Kogyo acts as a driving force to support the evolution of manufacturing technology at our overseas bases. For example, when trouble arises at an overseas base, we start by sharing information with relevant departments at the head office. In addition to detailed quality monitoring done every week, we have built a system for discussing solutions face to face when necessary, so that we can execute measures precisely and rapidly. We aim to not push the Japanese way of doing things on local staff, but realize a high level of quality together with our staff so that they can work independently.
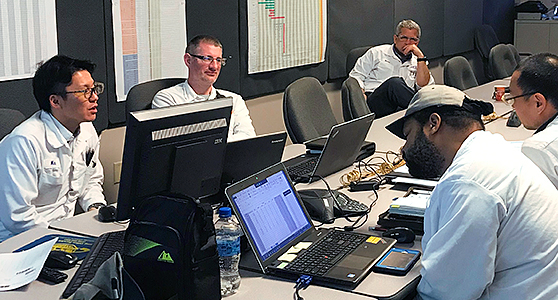
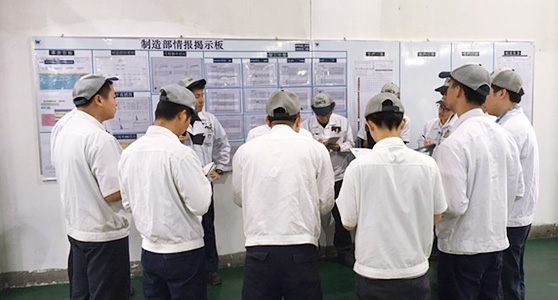