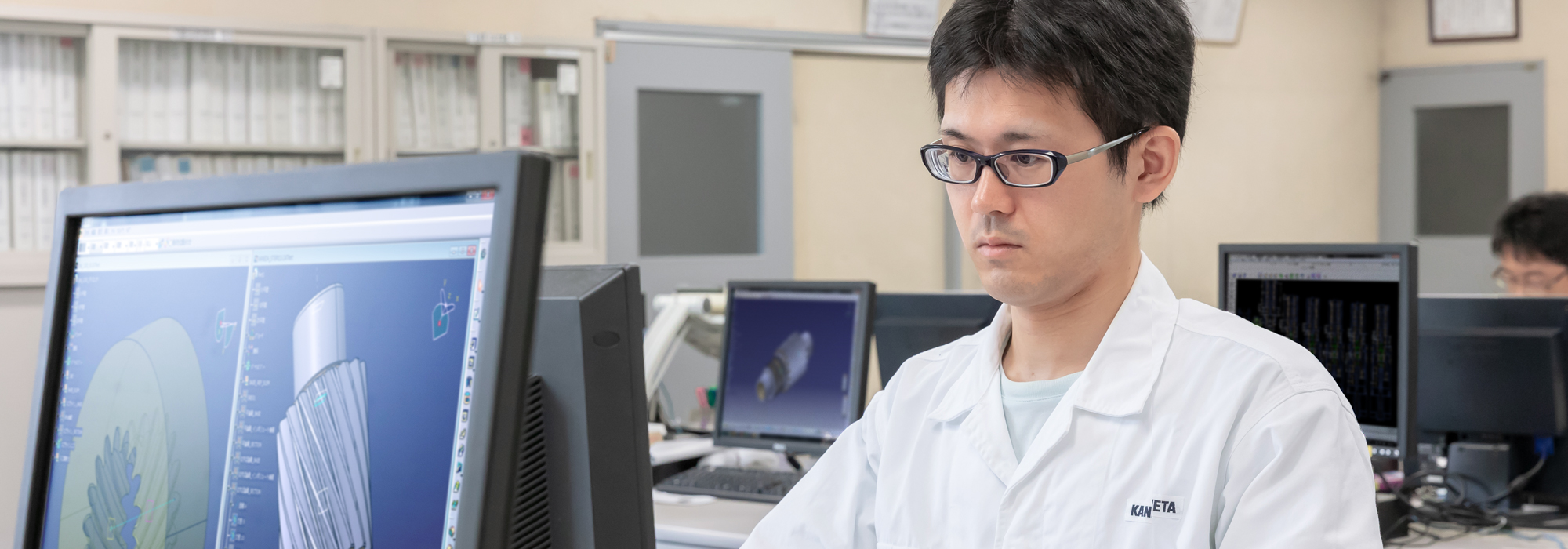
冷間鍛造シャフトの設計
ただの素材を「機能を持った」カタチに変える。
もの造りの面白さを凝縮した仕事。
松島 暢彦[2010年入社/機械工学専攻]
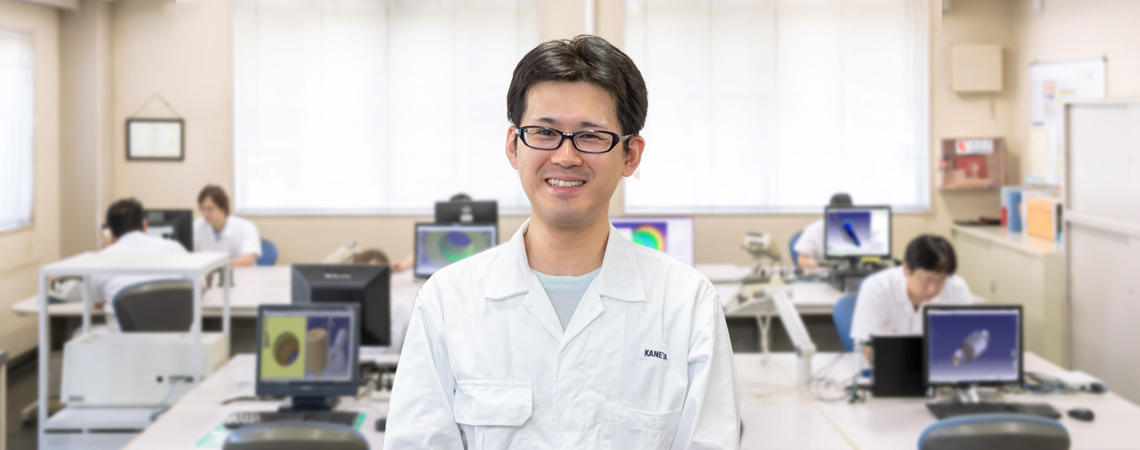
冷間鍛造の強みを造り込む
製造のプロセスを設計
私の所属する冷鍛技術課は、主に設計業務と不具合対応を担当しています。設計業務は大きく2つに分けることができて、鍛造のやり方や後加工など、どのように製品を造っていくかを考える「工程設計」と、その工程を反映した金型を造る「金型設計」があります。当課の使命は、確かな製品を生み出すのはもちろん、冷間鍛造の大きなメリットである高速生産・短納期、そしてそれによるコストダウンを実現して、お客様に喜んでいただくこと。コスト意識を常に持ち、これまでの経験と当社に蓄積されたノウハウを駆使して、常に最良の設計を目指しています。
もの造りをしているという実感
冷間鍛造は素材を何回かプレスしながらだんだん希望の形に仕上げていくのですが、素材や金型に無理をさせないようにして高精度な成型(塑性加工といいます)を行うためのノウハウがたくさんあります。さらに、当社の得意分野である長尺のシャフトは製品自体の重みで加工中にも微妙にたわむため、そういったエラー要因を抑え込みつつ1/100mm単位で精度を出していくのは、製品ごとに挑戦の連続です。しかし、何の変哲もない素材が自分の設計で「機能」を持った製品になっていくのは、まさにもの造りそのものという実感があります。
現場出身の設計者として
現在は設計を担当していますが、入社してすぐに設計に携わったのではなく、5年ほどオペレーターとして現場作業に従事していました。ですから、どんな形状の製品だと現場でどんな注意が必要なのか、どんな工程だと作業が行いやすいのかを肌で理解しているのが、自分の強みだと思っています。その経験を生かして、金型を造る人、生産設備を組む人、現場で作業する人、そしてメンテナンスをする人それぞれに配慮した工程設計を心掛け、当社の一貫体制の強みを競争力につなげるべく、日々仕事に取り組んでいます。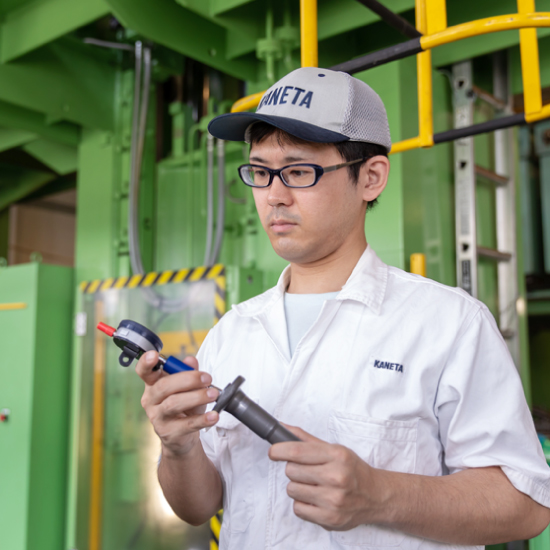
ノウハウを数値化し、社内の共有資産に
長年の経験があるといっても、「やってみなければわからない」部分がまだまだ残っているのが冷間鍛造の分野です。そこで当社では最新の解析ソフトを導入して、塑性変形のノウハウを数値化し、定量的に蓄積する取り組みを進めています。特に金型の製造技術は、未だに手から手へ継承されている部分が少なくありません。それも当社の資産のひとつではあるのですが、今後はその資産を誰もがスピーディーに活用できるよう、解析データの蓄積とCAEの習熟度の向上を進め、より高度で効率的な生産を目指していきます。
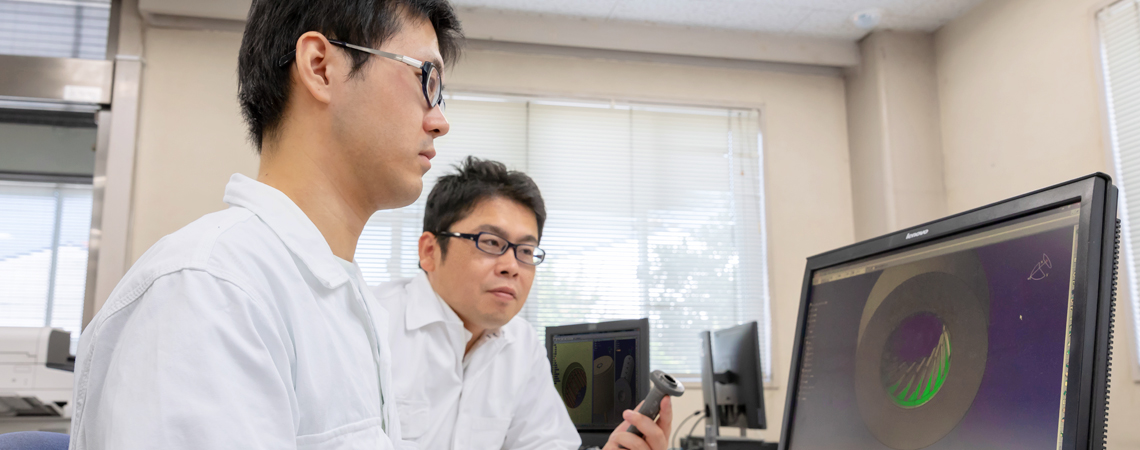