COLD FORGING

We keep costs low while also keeping products strong, precision high, and production fast.
The forging process does compression molding of metal materials using a strong mold and a strong former. By forging materials, it is possible to shape the “fiber flow” known as metal fiber and densify the structure, thereby making a product with high strength and excellent resistance to wear. Furthermore, Kaneta Kogyo’s specialty cold forging has many merits compared to hot forging, which works by heating materials, in that it makes for more precise dimensions and is capable of more rapid processing because it does not involve heating or cooling processes.
Kaneta Kogyo uses its wealth of knowledge accumulated over the years and the industry’s leading production equipment specialized in cold forging to propose new value for your company’s manufacturing process.
Kaneta Kogyo uses its wealth of knowledge accumulated over the years and the industry’s leading production equipment specialized in cold forging to propose new value for your company’s manufacturing process.
We reduce material and processing loss with near net shape processing.
This reduce costs from both materials and labor.
The shaft products representative of our company’s products are made by adding Kaneta’s unique development and production technology to the benefits of the cold forging manufacturing method (high rigidity, high precision, fast production). Rotating bodies are the core element of various kinds of mechanism. The shaft products that support the center of these rotating bodies must be strong and have excellent balance down to 1/1000th of a millimeter. From 2-wheel vehicles and 4-wheel vehicles including hybrids, all the way to construction machinery and general purpose equipment, Kaneta Kogyo’s cold forging technology serves a role in global quality.
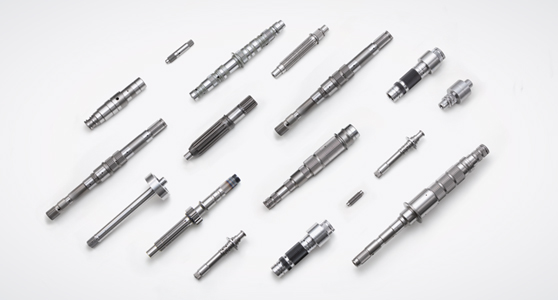
Because it is a room temperature process, it makes high speed and high precision production possible.
We meet demands for quality, cost, and delivery time at a higher level.
In addition to cold forging, representative methods of manufacturing machine parts include hot forging, casting, and machining from materials. Of these, cold forging is the method that demonstrates its strengths particularly well in mass production, and can meet the requirements of QCD in a well-balanced and high-level manner. It is a commonly used method for relatively small parts such as bolts and nuts because of the heavy burden on molds and formers. But, using our full range of production equipment including one of the world’s largest formers, Kaneta Kogyo has achieved success with the production of both short and long, small and large diameter products. This extends from a minimum cutting length of 20 mm to a maximum cutting length of 450 mm, and a minimum diameter of 9.05 mm to a maximum diameter of 47 mm (coil material) or a maximum diameter of 51 mm (blank material).
We have realized excellent mechanical properties by producing fiber flow that follows the product shape.
Forging, known as the method for crafting samurai swords, is a method of modifying the characteristics of metal material itself by repeatedly compressing metal. It is possible to give high strength and durability by cold forging, even with the same material and product shape. Converting to cold forging will make your company’s product more competitive.
Metal microstructure flow lines.
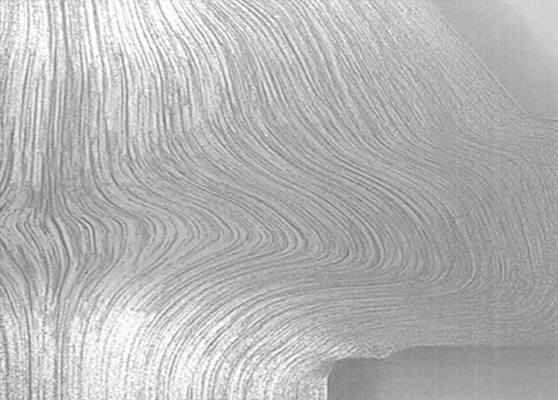
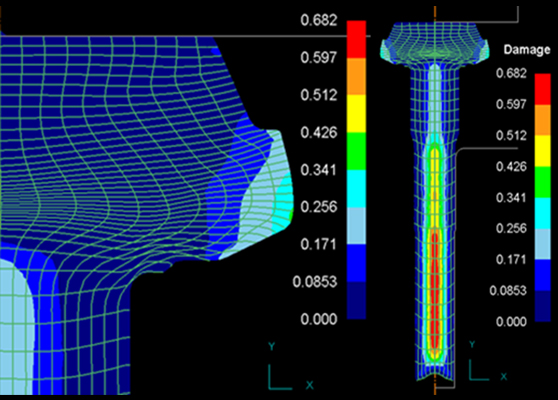
Kaneta-ism is alive in our production facilities.
We conduct some mold making and polishing of cutting tools in house.
Kaneta has technology and equipment capable of manufacturing molds in house, except for some molds which require special equipment. Not only can we reflect our deep knowledge of products and processes directly on molds; we can also apply our unique knowledge to precision lapping and regular maintenance.
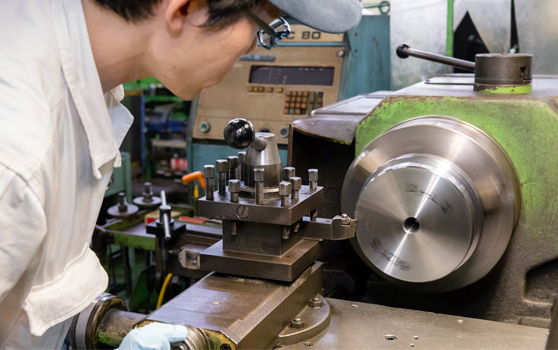
Manufacturing method conversion contributes to reducing man-hours and costs.
Kaneta Kogyo is defined by its wide range of capabilities, from mass production to specialized products. Our specialty is manufacturing of shafts. Shafts must have excellent drive performance and durability, and these are also highly specialized parts that require ultra-precision machining of complex shapes. Based on our experience in supplying thousands of parts for 2-wheel and 4-wheel vehicles and general purpose equipment, we make a range of proposals to reduce the number of processes and their cost using cold forging technology.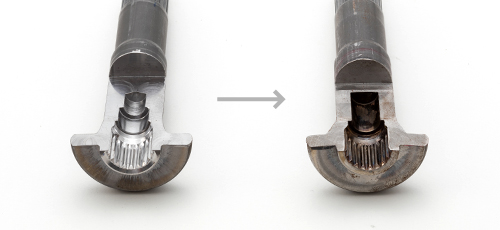
We reduce materials and processes with integral formation of deep holes and inside diameter splines using cold forging.